Understanding the Dynamics of Injection Molding: A Comprehensive Guide
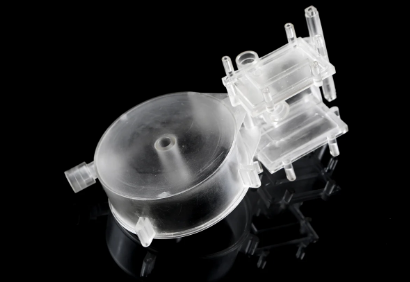
In the world of manufacturing, injection molding stands as a cornerstone process, revolutionizing the way we produce plastic and other materials. This article delves into the intricacies of injection molding, exploring its history, process, applications, and advancements.
I. A Brief History of Injection Molding
A. Inception and Evolution
Injection molding traces its roots back to the late 19th century when Alexander Parkes invented Parkesine, a precursor to plastic. However, it wasn’t until the 20th century that injection molding gained prominence, with the development of the first injection molding machine by John Wesley Hyatt in 1872.
B. Technological Milestones
Over the years, injection molding has undergone significant technological advancements. The introduction of electric injection molding machines, computer numerical control (CNC) systems, and sophisticated mold designs has propelled the industry forward, enhancing efficiency and precision.
II. The Injection Molding Process
A. Basics of Injection Molding
Injection Molding involves the creation of three-dimensional products by injecting molten material into a mold cavity. The process comprises several key steps, including material preparation, injection, cooling, and ejection.
B. Materials Used in Injection Molding
The versatility of injection molding lies in its ability to handle a wide range of materials. Plastics, metals, ceramics, and even certain types of rubber can be used in the process. Each material comes with its unique characteristics, influencing the choice based on the desired end product.
C. The Injection Molding Machine
The heart of the injection molding process is the injection molding machine. These machines vary in size and complexity, but they all share the common goal of melting and injecting the material into the mold. Modern machines are equipped with advanced features like automation, real-time monitoring, and energy-efficient technologies.
D. Mold Design and Considerations
Successful injection molding relies heavily on the design of the mold. Factors such as cooling channels, gate placement, and part geometry play a crucial role in determining the quality and efficiency of the manufacturing process. Mold design has become a specialized field, with engineers utilizing computer-aided design (CAD) tools to optimize their creations.
III. Applications of Injection Molding
A. Automotive Industry
Injection molding plays a pivotal role in the automotive sector, producing various components like dashboards, bumpers, and interior trims. The process’s ability to create intricate and durable parts makes it a preferred choice for automotive manufacturers.
B. Consumer Goods
From household items to electronic devices, injection molding is ubiquitous in the production of consumer goods. The process enables mass production of consistent and high-quality items, meeting the demands of a diverse market.
C. Medical Devices
The healthcare industry benefits significantly from injection molding, producing medical devices with precision and reliability. Sterility, biocompatibility, and intricate designs are achievable through this process, making it integral to the production of items like syringes, vials, and implants.
D. Packaging Industry
Injection molding is a key player in the packaging industry, producing containers, caps, and closures with efficiency and cost-effectiveness. The process allows for the creation of lightweight and durable packaging solutions, contributing to sustainability efforts.
IV. Advancements in Injection Molding Technology
A. Industry 4.0 Integration
The advent of Industry 4.0 has brought about a new era in manufacturing, and injection molding is no exception. Smart, interconnected machines now allow for real-time monitoring, predictive maintenance, and data-driven decision-making, enhancing overall efficiency and reducing downtime.
B. Sustainable Practices
As environmental concerns grow, the injection molding industry is adapting to more sustainable practices. The development of bio-based and recycled materials, coupled with energy-efficient machines, reflects a commitment to reducing the environmental impact of manufacturing processes.
C. 3D Printing and Injection Molding Integration
The integration of 3D printing and injection molding presents exciting possibilities for the industry. Prototyping, mold design validation, and the production of complex geometries are facilitated by combining these technologies, pushing the boundaries of what is achievable in injection molding.
V. Challenges and Future Outlook
A. Challenges in Injection Molding
Despite its widespread use and success, injection molding faces challenges such as material waste, energy consumption, and the need for skilled personnel. Ongoing research and development aim to address these issues and further optimize the process.
B. Future Trends
The future of injection molding looks promising with ongoing research in areas such as artificial intelligence, material science, and robotics. The industry is poised to become more adaptive, sustainable, and capable of meeting the evolving demands of diverse markets.
Conclusion
In conclusion, injection molding has evolved from a rudimentary process to a sophisticated and indispensable manufacturing technique. Its impact on various industries, coupled with ongoing technological advancements, positions injection molding as a key player in the ever-changing landscape of modern manufacturing. As the industry continues to innovate, the possibilities for injection molding are boundless, ensuring its relevance in the production of tomorrow’s products.