The Role of Industrial Blenders in Modern Manufacturing Processes
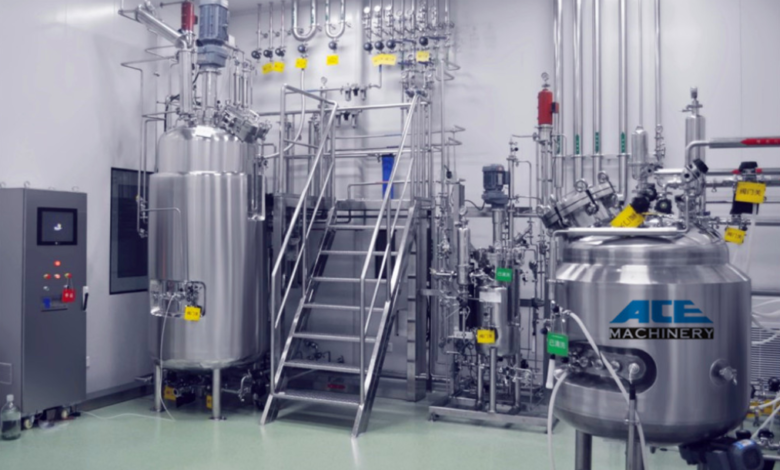
Key Takeaways
- Industrial blenders significantly improve manufacturing efficiency and consistency.
- Customization and versatility make them adaptable to various industries.
- Knowledge of their functionality aids in informed purchasing and operational decisions.
Industrial blenders have emerged as indispensable tools across various manufacturing sectors. These sophisticated machines are pivotal in improving efficiency and consistency, which are crucial for achieving high-quality production standards. From pharmaceuticals to food processing and chemical manufacturing, the presence of an efficient blending machine is fundamental to creating homogeneous mixtures that are both reliable and effective. Selecting and utilizing the right industrial blender involves a keen understanding of its functionalities and applications, ensuring that any operational decisions made are informed and strategically sound.
The ability to customize these machines to meet specific production needs adds to their appeal. Customization allows companies to tailor the blenders to their unique operational environments, enhancing productivity and ensuring that the outputs meet the desired quality standards. Understanding the role and benefits of industrial blenders can help businesses optimize their manufacturing processes, reduce waste, and save on costs while maintaining the highest standards of product quality and safety.
What Are Industrial Blenders?
At their core, industrial blenders are machines designed for mixing and homogenizing substances within manufacturing settings. They operate through mechanical action, which allows for thoroughly blending materials ranging from powders and granules to emulsions and pastes. These blenders are not one-size-fits-all; numerous types are designed to cater to the unique needs of different industries. This flexibility makes them an invaluable addition to any production line requiring consistent and efficient mixing processes, ensuring that the end products meet stringent quality standards for commercial success.
Why Are Industrial Blenders Essential in Manufacturing?
Industrial blenders bring unmatched efficiency and consistency, making them indispensable in manufacturing. They ensure precise and uniform mixing, critical in sectors like food and pharmaceuticals. For example, in the pharmaceutical industry, it’s paramount that every pill has an exact dosage of active ingredients. This level of precision can only be achieved through the use of well-calibrated industrial blenders that are tailored to produce consistent mixtures. Such expertise in blending enhances product reliability and builds consumer trust in the brand. Industries heavily rely on these machines as they streamline production processes while upholding quality standards.
Types of Industrial Blenders
Ribbon Blenders
Ribbon blenders are known for their efficiency in achieving homogeneous mixtures, particularly for dry powders and granular materials. Their design incorporates a sizeable ribbon-like blade that moves material within the blender, ensuring comprehensive mixing quickly. This type of blender is ideal for applications that require a gentle yet effective blending action, minimizing the breakdown of the delicate components being mixed.
V-Blenders
V-blenders are uniquely structured to handle delicate blends and offer a gentler mixing process. They are characterized by their V-shaped design, which promotes tumbling action and ensures a thorough blend without causing damage to the ingredients. This makes them particularly suitable for fragile materials or mixtures that are sensitive to mechanical stress, such as certain powders used in pharmaceuticals and food processing.
Double Cone Blenders
These blenders are handy for mixing free-flowing granules and powders. The double-cone design facilitates even blending by allowing materials to cascade through the cones as the blender rotates. Their ability to mix quickly and evenly makes them an excellent choice for industries that require rapid production cycles without compromising the quality of the mixture.
Key Features to Consider When Choosing an Industrial Blender
When choosing an industrial blender, several features need to be considered. The machine’s capacity determines the amount of material that can be processed simultaneously, which is essential for achieving production goals. The blender’s longevity and suitability for handling various chemicals are influenced by its construction material, particularly in settings with strict hygienic regulations. Another crucial factor is ease of cleaning, especially in sectors where sanitation is critical, like the food and pharmaceutical industries. Furthermore, these blenders’ usability is improved by customization, which enables companies to modify them to fit particular jobs and procedures. Making well-informed judgments suited to different operating requirements can be further aided by trustworthy advice on selecting the best blender.
Benefits of Using High-Quality Industrial Blenders
Investing in high-quality industrial blenders offers a multitude of benefits. They significantly improve product quality by ensuring consistent mixes, reducing material wastage, and fostering a more cost-effective manufacturing process. High-quality blenders are engineered to withstand the rigors of continuous operation, ensuring that production lines maintain their efficiency without frequent breakdowns or maintenance interruptions. This durability, combined with precision and speed, makes a compelling case for why they are worth the investment, ensuring long-term benefits that enhance productivity and profitability.
Real-Life Examples: How Industries Benefit
In the food industry, for example, consistently blending ingredients like spices ensures each product tastes the same, anchoring brand reliability and consumer trust. Meanwhile, even minor mixing inconsistencies can significantly affect drug efficacy in the pharmaceutical sector. Each tablet must have uniform consistency to guarantee the correct dosages and therapeutic effects. Case studies from these industries highlight the essential role of industrial blenders in ensuring these standards are met, providing firsthand accounts of enhanced efficiency and product quality achieved through the precise operation of these machines.
Future of Industrial Blending in Manufacturing
Looking toward the future, the evolution of industrial blenders will be shaped by ongoing technological advancements. Trends center around automation and integration with digital systems, enhancing the precision of blending operations while reducing human intervention. Emerging technologies enable machines to self-monitor and adjust mixing parameters dynamically, ensuring optimal performance at all times. These advancements are set to revolutionize traditional manufacturing processes, making them more efficient and adaptable. Manufacturers seeking to stay ahead must pay attention to these industrial equipment trends, as they represent the driving force behind future operational improvements.
Conclusion
In conclusion, industrial blenders are indispensable in modern manufacturing processes, offering unmatched benefits that enhance efficiency and product quality. By understanding their functionalities and roles across different sectors, businesses can make strategic decisions that align with their long-term objectives. The future of manufacturing will undoubtedly see further integration of advanced blending technologies, reinforcing these machines’ vital role in shaping efficient and innovative production strategies.